Process Engineering
Process Engineering
Catalysts are used in more than 80% of industrial processes for carrying out chemical reactions. A catalyst increases the reaction rate and improves the yield of a chemical reaction without being consumed itself. Due to the different processes and associated catalyst forms, there is a wide range of chemical reactors and apparatus in which the catalytic processes can be carried out safely and economically.
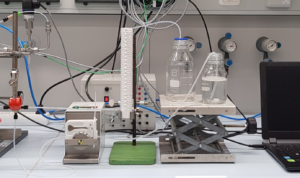
Experimental setup with capillary spiral reactor for gas-liquid biocatalysis with pumps, bubble generation, FEP capillary tube and measurement data acquisition
©Apparatedesign, TU Dortmund
In addition to efficient contact and mixing of the reactants with the catalyst, heat transfer and flow control with narrow dwell time distribution of the reagents play a major role in reactor selection. The reactants must be prepared according to the reaction conditions and the resulting reaction mixture must be processed. Often, the optimal separation and recirculation of reaction partners or catalyst material determine the economic efficiency of a process.
Process development for a particular product begins in the laboratory with many trials accompanied by analytical development and simulations. A successfully optimized process is then scaled up to pilot scale and often through several steps to production. Already in the laboratory, but even more so at pilot scale, suitable sensors and analytics as well as the process control system for optimal process control play an increasingly important role. A variety of separation processes are available for separating the reaction mixture, depending on the phases of the components involved, concentrations in the mixture and the energy required. Also here, recirculation, optimal energy and material flow integration are important for economical process control.